The Journey of Harvesting Laurel Oak
- Bradley Eklund
- Sep 27, 2024
- 4 min read
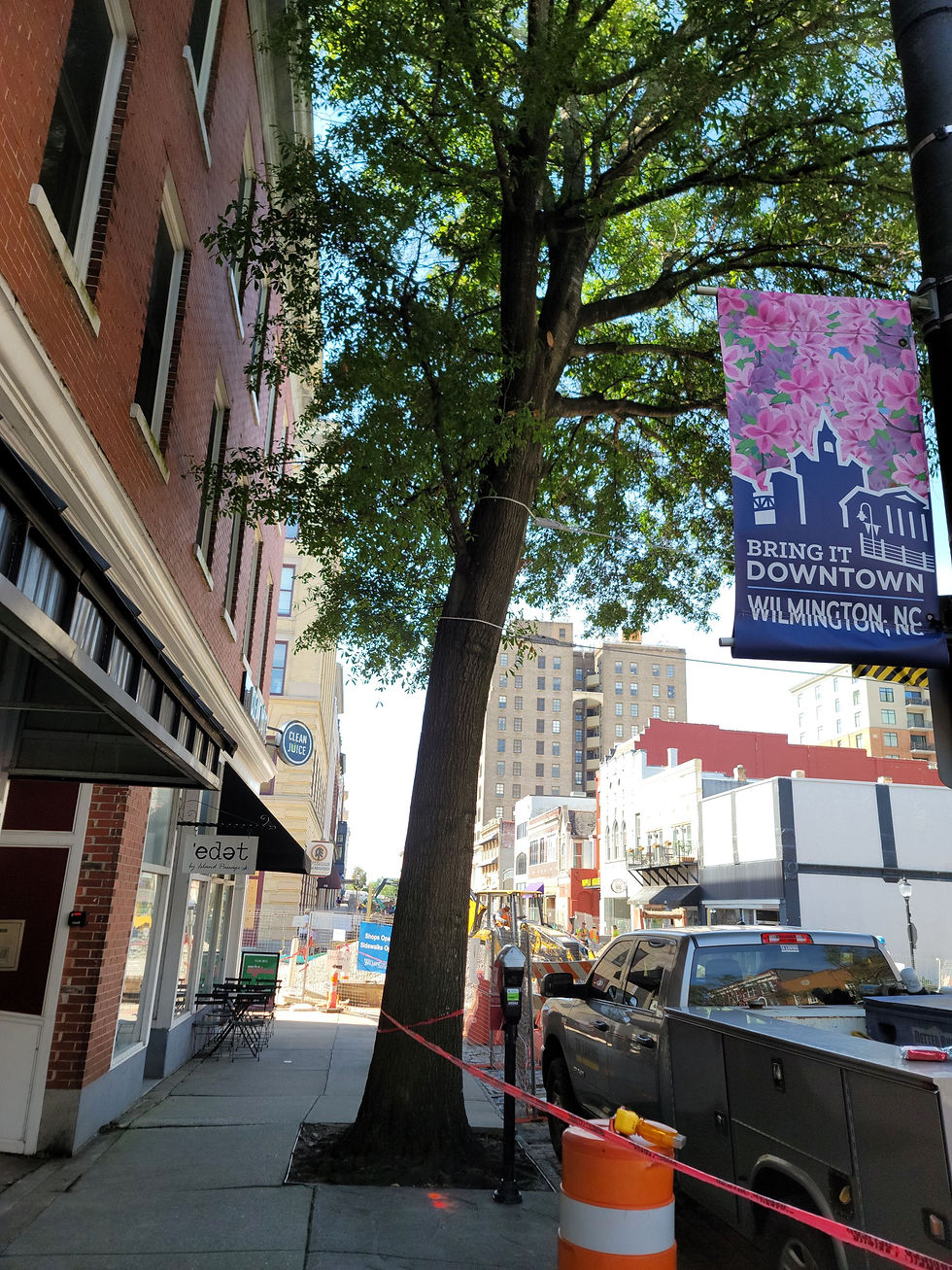
When a tree falls naturally or must be removed for important reasons, it presents a unique opportunity to sustainably harvest its wood. This gives the tree a second life by transforming them into beautiful, timeless creations to be enjoyed for many years after the tree is gone. In this blog post, we'll walk you through the process of how we came across one such opportunity to harvest some local oaks.
Oak is a very common hardwood found all throughout North America and many other regions. It has a reputation for being a durable, strong wood. For the most part, oak lumber is divided into two types: red oak and white oak. Many different species fall into each group but one species in particular stands out to me and that species is Quercus laurifolia, also known as Laurel Oak. Never heard of it? That is no surprise as it rarely finds its way into domestic lumber, but it has some characteristics suited perfectly for intarsia and other scroll saw projects.


In 2022, some major road construction was scheduled just outside of a local artist co-op gift shop that I’ve been involved with since 2011 called Port City Pottery and Fine Crafts. This shop is one of many located inside of a historic repurposed building called The Cotton Exchange. The new improvements was exciting. That excitement turned to dismay when we learned that several decent sized oak trees would have to come down due to the work. We love trees and it's always a shame when one needs to come down. Our kids grew up running circles around these trees.


Then a thought popped into my head. If we can’t save them from getting cut down, then maybe we can save them from the landfill. When I first entertained the idea, I thought there was no way the parties involved would work with me to salvage the trees. I spoke with the building manager for The Cotton Exchange who absolutely loved the idea. She put me in touch with the project coordinator for the city who also loved the idea. Afterwards, he spoke to the person leading the construction who gave the green light, and I was left completely dumb struck. “Holy cow! This is actually happening!” I had no idea what I was getting myself into! When I pitched the idea, I told them I only wanted 1 or 2 trees (thinking that would minimize any inconvenience). They called me back to go over details and then asked if we would take 10 trees in total! A single tree would last us years. 10 trees would ensure a lifetime supply of oak!
Time to get busy planning! I had to find a sawmill capable of milling large logs. I needed to hire a flatbed truck to transport the logs to the sawmill. Then the impossible task of making room in my garage to store the boards. Moving tools, wood, shelves…there was a ton of prep!


When milling day rolled around, I was so excited. I’ve never seen a log milled in person and jumped at the chance to go and see the process up close. If you have never seen a sawmill in the works, I recommend doing so if you get the chance. As each slab was cut, I noticed something that I didn’t expect. This wood didn’t look like any oak I’ve ever used in the 10+ years of woodworking. Some sections were white. Others were red. While others had a swirling splash of grey coloring. So many colors all from the same kind of tree. FYI, these specific trees were laurel oaks which belong to the red oak group and, previously unknown to me, tend to have more varied coloration. Laurel oaks are not the typical oak species harvested for regular lumber.

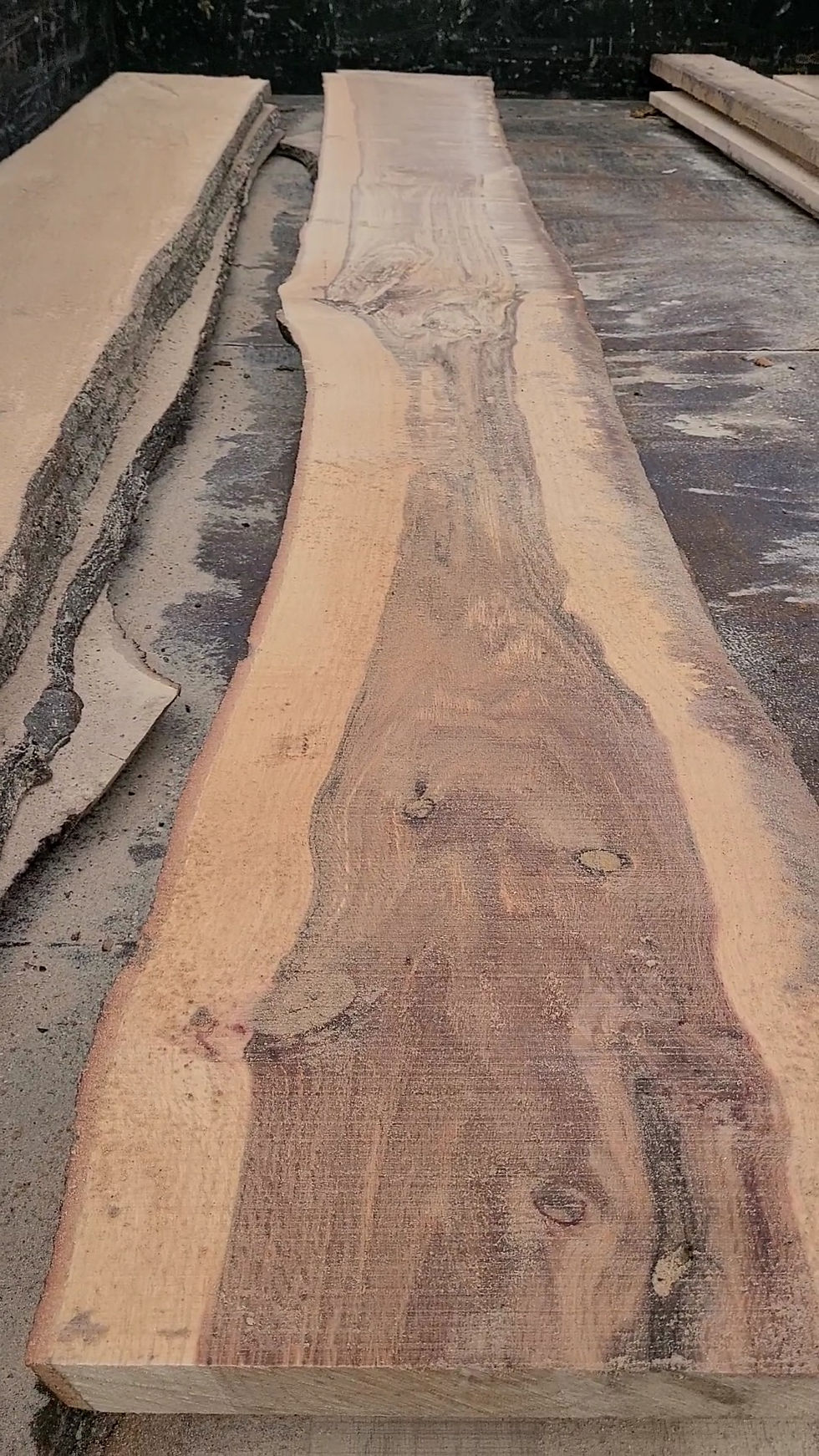
Drying and properly stacking lumber is critical. Each layer needs exposure to air. Ends of boards should be sealed to prevent cracking. Lots, and I mean lots of weight needs to be placed on top to prevent the wood from bowing. It was backbreaking work for sure. Both Hazel and I slept very well for several nights in a row. The hardest part of everything was after all the work put into making all this happen, I couldn’t use a single piece of wood. With the lumber being air dried in the garage, it took close to a year for the moisture content to reach a usable level.
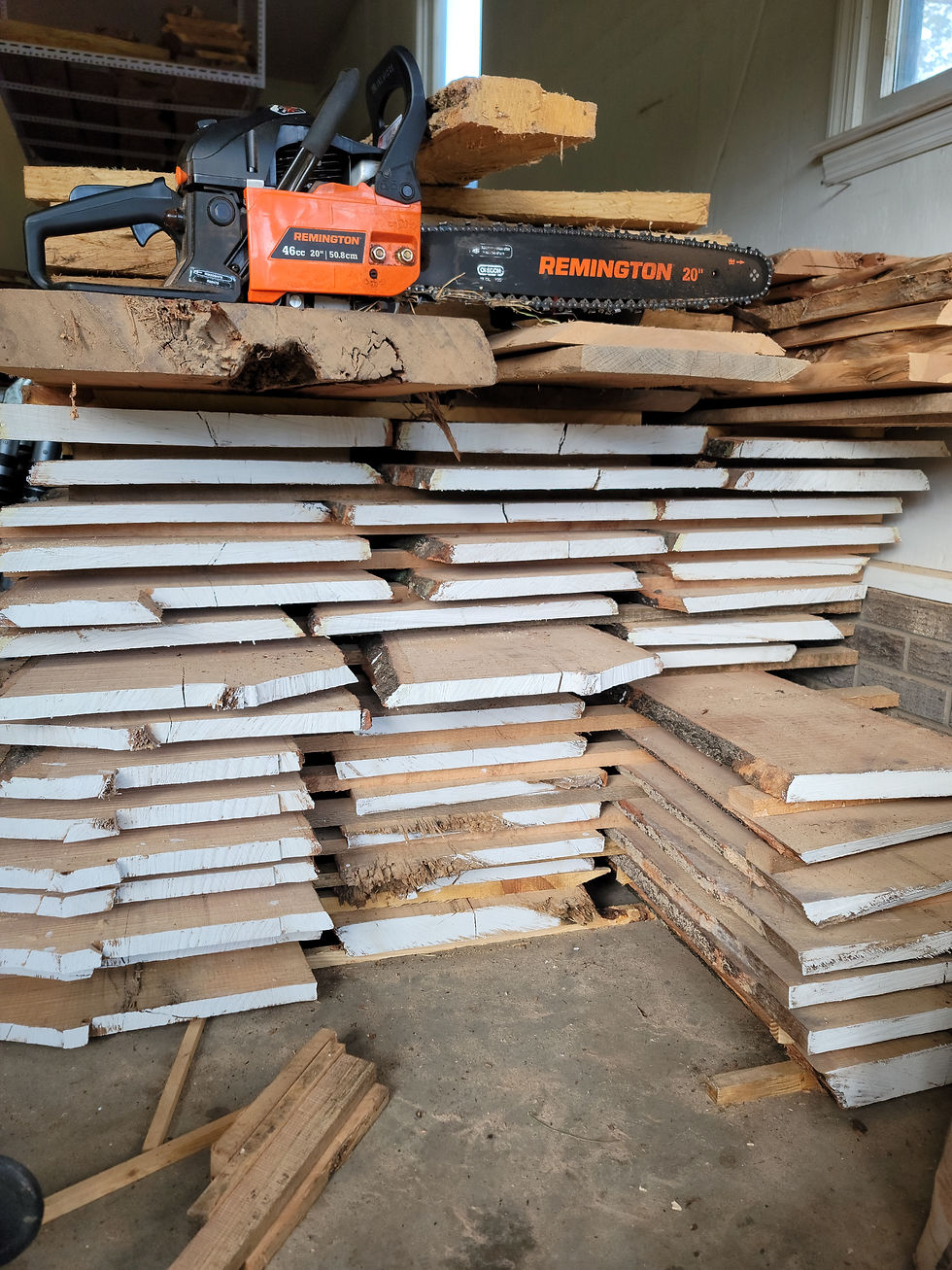

It was worth the wait though. We have used a significant number of boards, but each one is always unique. You never know what the board will look like until it’s planed smooth. I also made a fun discovery. Several boards had a thick layer of sawdust from the milling process. This caused some (not all) boards to spalt, creating some eye-catching streaks.
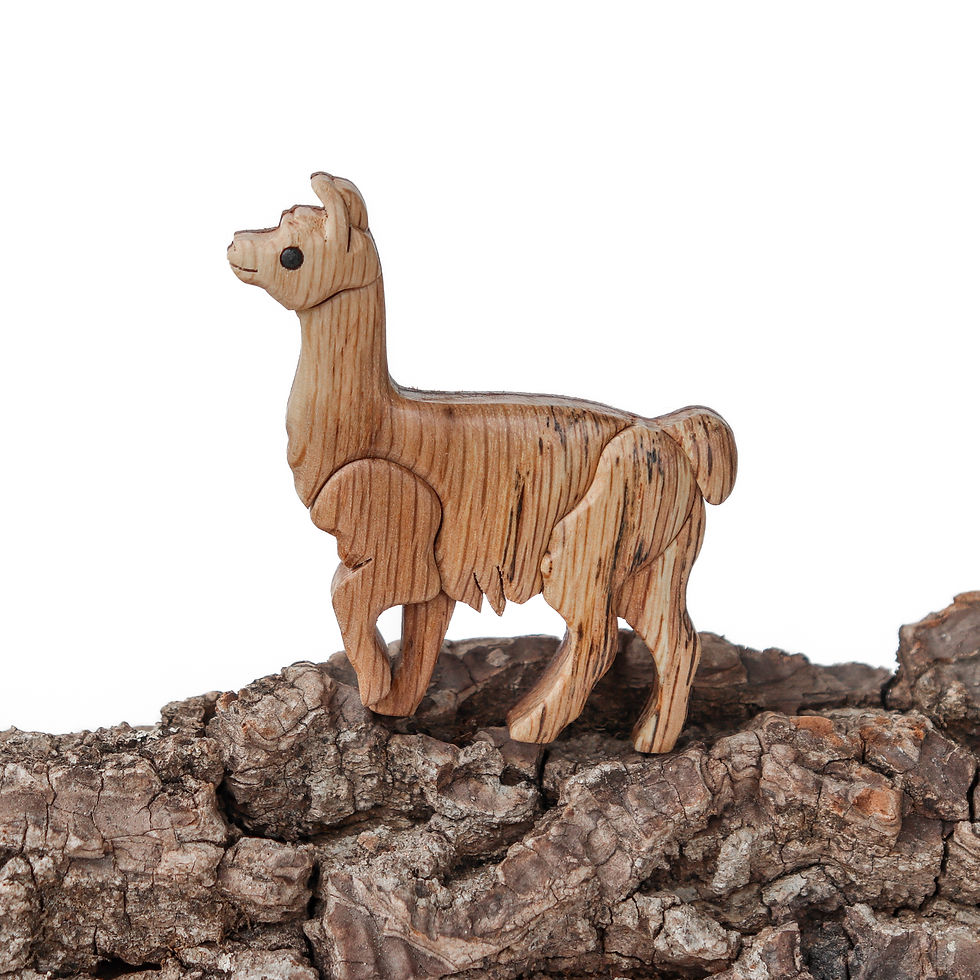
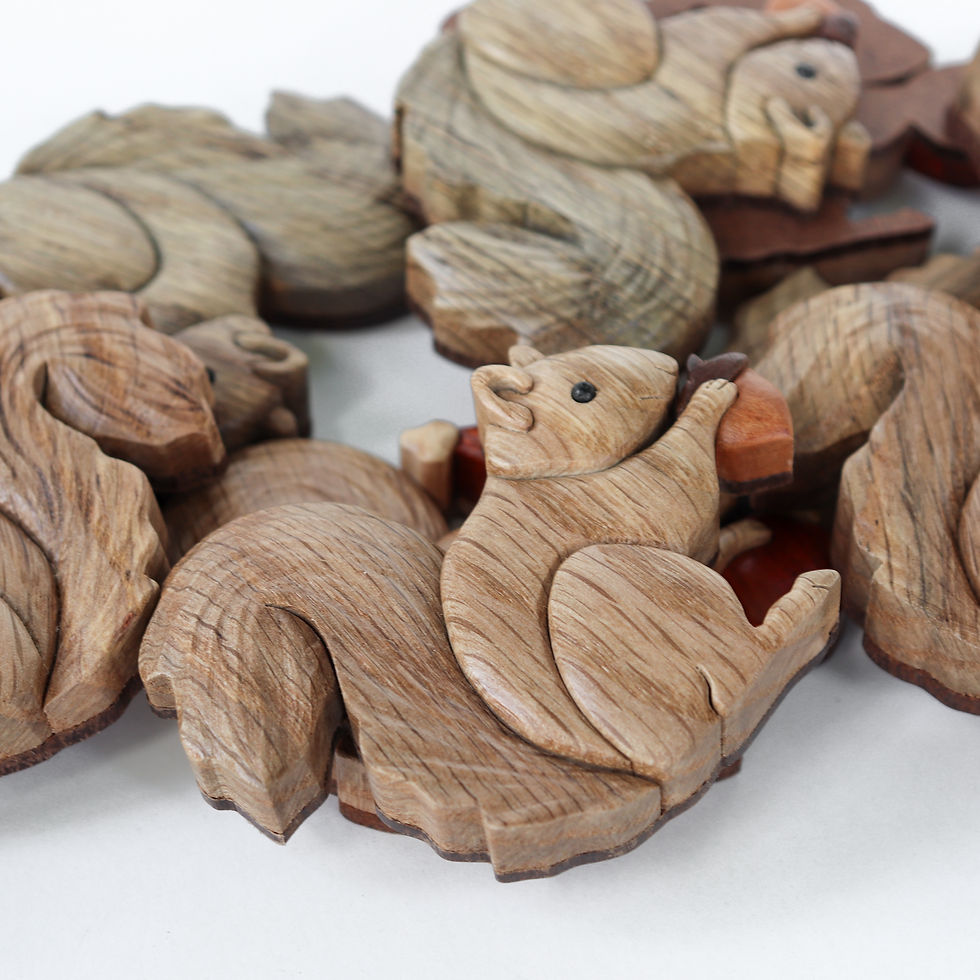
Needless to say, you will find some oak in many of our projects. Since the wood varies so much, that’s not too hard to do. The wood also takes stain very well and we use it when we dye wood green or blue. To top things off, the wood ebonizes very well and gives a light grey to a dark grey color depending on the board and strength of the ebonizing solution.


Before harvesting these trees, I always considered oak a rather boring wood. I now have an entirely new level of appreciation for this incredible species. I’m very grateful that all parties were so supportive. While it's a shame that the trees had to come down, I'm very happy that we saved them from the landfill. The community was also thankful and I was interviewed by a local news company about the whole process. I like to share stories of the wood we use and it always peaks interest when we tell customers and admirers that the item they are holding was made from a tree that use to grow right outside the building. By harvesting lumber locally, we're not only embracing the beauty and strength of this incredible wood, but also supporting sustainable practices that weaves together our passion for nature and craftsmanship.
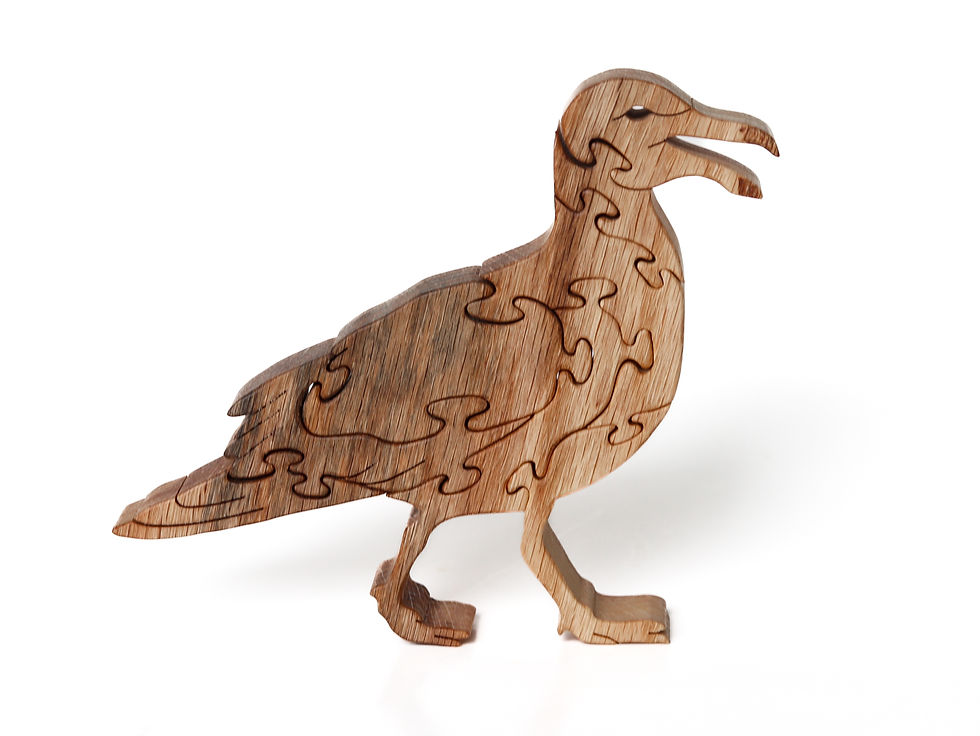
We hope you enjoyed reading this blogpost. If you're new to our blog, be sure to subscribe and check out our monthly "Pattern Subscription" plan. It's a great value giving access to a growing number of free patterns.
תגובות